Reduced Order Modelling
Simplifying modelling
In multibody system simulations the question often arises how to model the behavior of complex mechanical structures accurately. Reduced Order Modelling provides an answer.
In multibody system simulation, the main areas of interest may be the overall system behavior during operation and the electric/hydraulic power transmission performance. For such analyses to be successful, the relevant behavior of all components must be caught accurately in the simulation model. This can be specifically difficult for complex mechanical structures in the system.
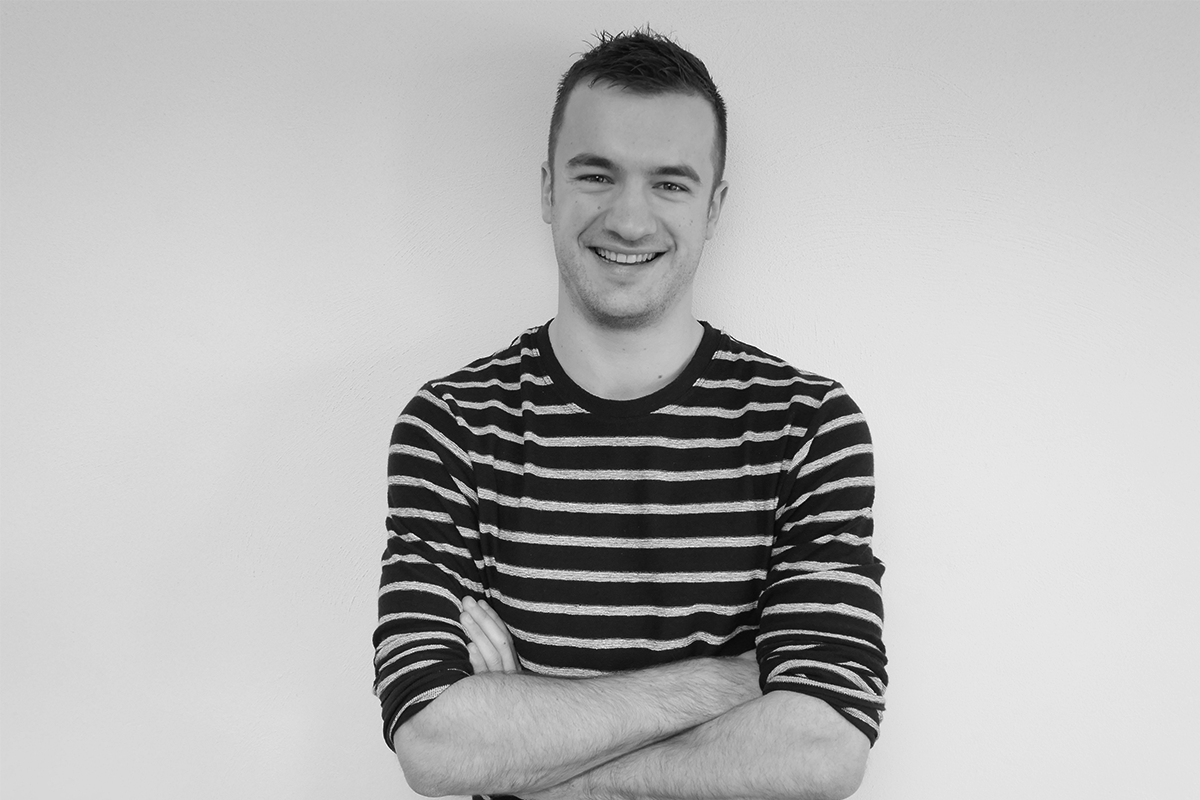
Jeroen Ligthart
Lead Engineer Simulation
"Via Reduced Order Modeling the size of the model is reduced significantly, while the relevant overall system behavior is maintained."
Combining FEM and Simulink
When the behavior in a mechanical structure acts over just a single dimension, a lumped-mass modeling approach may be applied. Even for such a ‘simple’ component it can be a challenge to determine realistic masses and stiffnesses. For systems that act over multiple DOFs, from truss constructions to steel castings, a lumped-mass modeling approach may not be a viable option. An alternative modeling technique that can be used for these type of components is a Reduced Order Modelling (ROM) approach.
Reduced Order Modelling
With Finite Element Method (FEM), the behavior of a complex structure can be analysed accurately up to the local stress distributions. For multibody system simulations a FEM modeling approach is not applicable since the computational load of such models is far too large. To overcome that problem a Reduced Order Modelling (ROM) approach can be applied based on a FEM model. Via ROM the size of the model is reduced significantly, while the relevant overall system behavior is maintained. Some local behavior will be lost, such as the aforementioned local stress distributions, but this is acceptable, as that is not relevant to the multibody simulation. Instead the overall system behavior, so the mass-, inertia-, and stiffness distributions, is maintained.
ROM in a digital twin
In the development of the Digital Twin for the Hydrohammer, HVR Engineering applied a Reduced Order Modelling approach to increase the accuracy of modelling the impact behavior of a hydraulic piling hammer on XL monopiles. While the impact behavior of the ram and the pile can be modeled reasonably accurate with a lumped-mass approach, this is not true for the anvil (the component that transfers the energy from hammer to pile). The latest generation anvils, capable of driving 6.5 meters monopiles, and the next generation anvils for 8 meter monopiles, will see significant bending under the impact force due to these large diameters. Accurately modeling the complex deformation of the anvil has been achieved by using a Reduced Order Modelling Approach.
HVR has submitted a paper on ROM modeling approach for Piling Hammer Anvils for the ‘11th International Conference on Stress Wave Theory and Design and Testing Methods for Deep Foundations’. This paper will be shared on the website after if it is accepted and published.

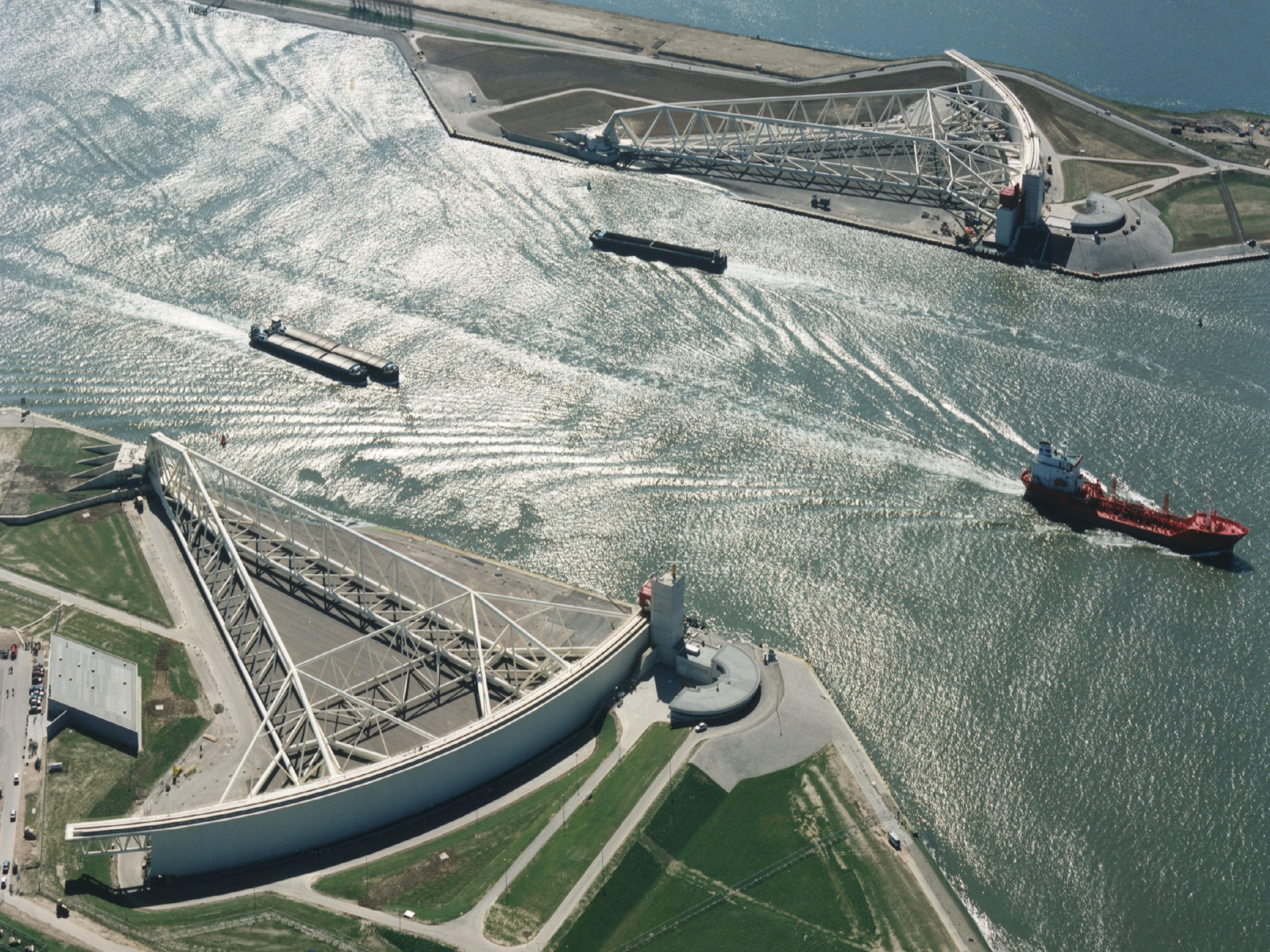
ROM at the Maeslantkering
We apply Reduced Order Models in the Maeslantkering simulation model. Read more about how we approach this project.
How we can help you
At HVR Engineering we constantly push to apply new methods to solve complex behavioral analysis in a pragmatic way. We can combine extensive knowledge of strength and fatigue with behavioral simulation capabilities in Matlab Simulink.
Read more about how we can help you on our FEM and Simulations pages.