Offshore Transport Analysis
Offshore Transportation
Transportation of substructures used for offshore wind farms are often executed via sea on heavy lift vessels. Understanding the effects of transport operations on the fatigue life of a structure is essential to avoid premature failures of the foundation and to limit the conservatism of the foundation design for cost reduction purposes.
Currently there are two main types of substructures used in the industry, the Monopile and Jacket structures. Monopiles are typically transported horizontally, whereas the jackets are transported vertically. Due to the higher center of gravity of jackets the forces and moments on sea fastening during transport is to be analyzed thoroughly.
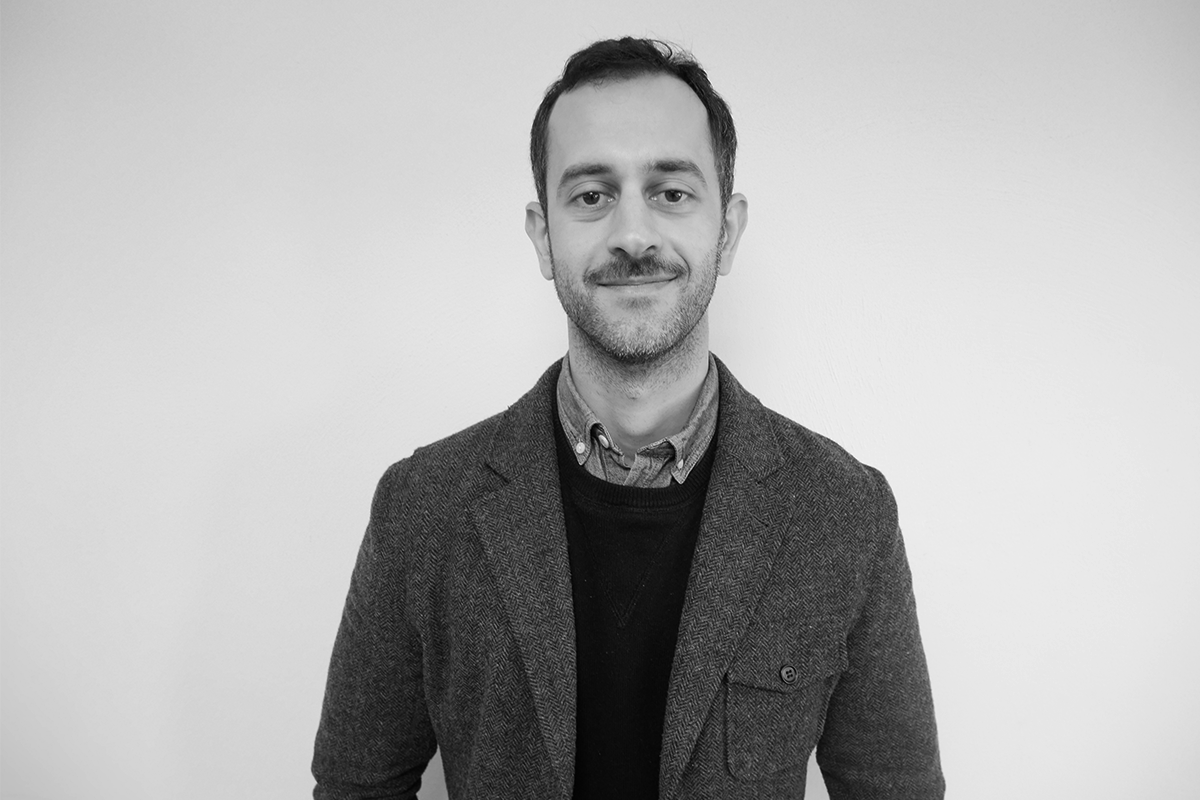
Michele Orlando
Lead Engineer Strength and Fatigue
"Understanding the effects of transport operations on the fatigue life in of a structure is essential to avoid premature failures of the foundation."
Diffraction Analysis
In order to have a good characterization of the forces acting on a jacket during transport, it is essential to include the vessel motion effects during sea voyage. There are several methods to approach a transport analysis of jackets and include these effects. One is by making use of a diffraction analysis to calculate the response amplitude operators (RAOs) that determine the behavior of a vessel in a certain sea state, under certain assumptions (e.g. small forward speed, incompressible fluid, small amplitude wave train). To accurately determine the RAOs the following information is needed:
- Vessel geometry and details, such as mass, center of mass, water line and moment of inertia along the 3 axis (roll, yaw, pitch) of the vessel.
- Details of additional deck equipment / transported structures, such as weights, center of masses, and moments of inertia.
Once the RAOs of the vessel are known, hydrodynamic analysis can be used to determine its behavior during the sea voyage and therefore the actions exerted on the jacket.
Hydrodynamic Analysis
Hydrodynamic analysis is used to define the accelerations of the vessel and the loads acting on the structure that is to be analysed. By using the RAOs the vessel’s response to external loading (sea state) is defined. For irregular loads multi-directional wave spectra can be used such as the JONSWAP or the Pierson-Moskowitz one. To select the necessary inputs representative of the studied transport operation, data from the Global Wave Statistics can be used.
Fatigue Analysis
A next step would be to define the effects of inertia loads on the structure. This can be done by global modelling to determine the most critical locations in the structure, and then use local models to define the Stress Concentration Factors (SCFs) of these locations.
Once the loads and the SCFs have been calculated, a Fatigue Analysis can be used to determine the fatigue on the structure during transport:
- In the frequency domain
- In the time domain.
Typically the frequency domain would be used initially since it is the simpler and faster solution. However, frequency domain analyses are based, and therefore limited to, linear assumptions. In case of non-linearity, such as plasticity or change in contact status on the analysed assembly – e.g. loss of contact at sea-fastening location, a time domain analysis is needed and the frequency spectrum will be converted appropriately into time traces for rainflow analysis
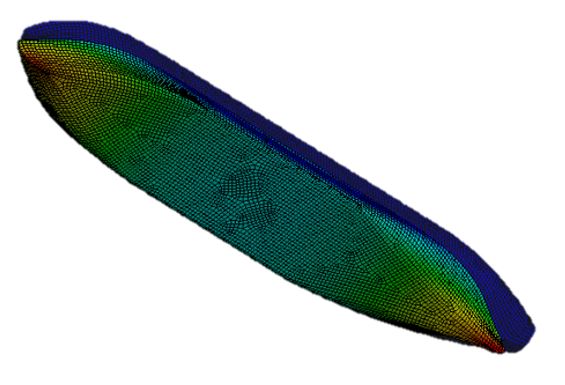
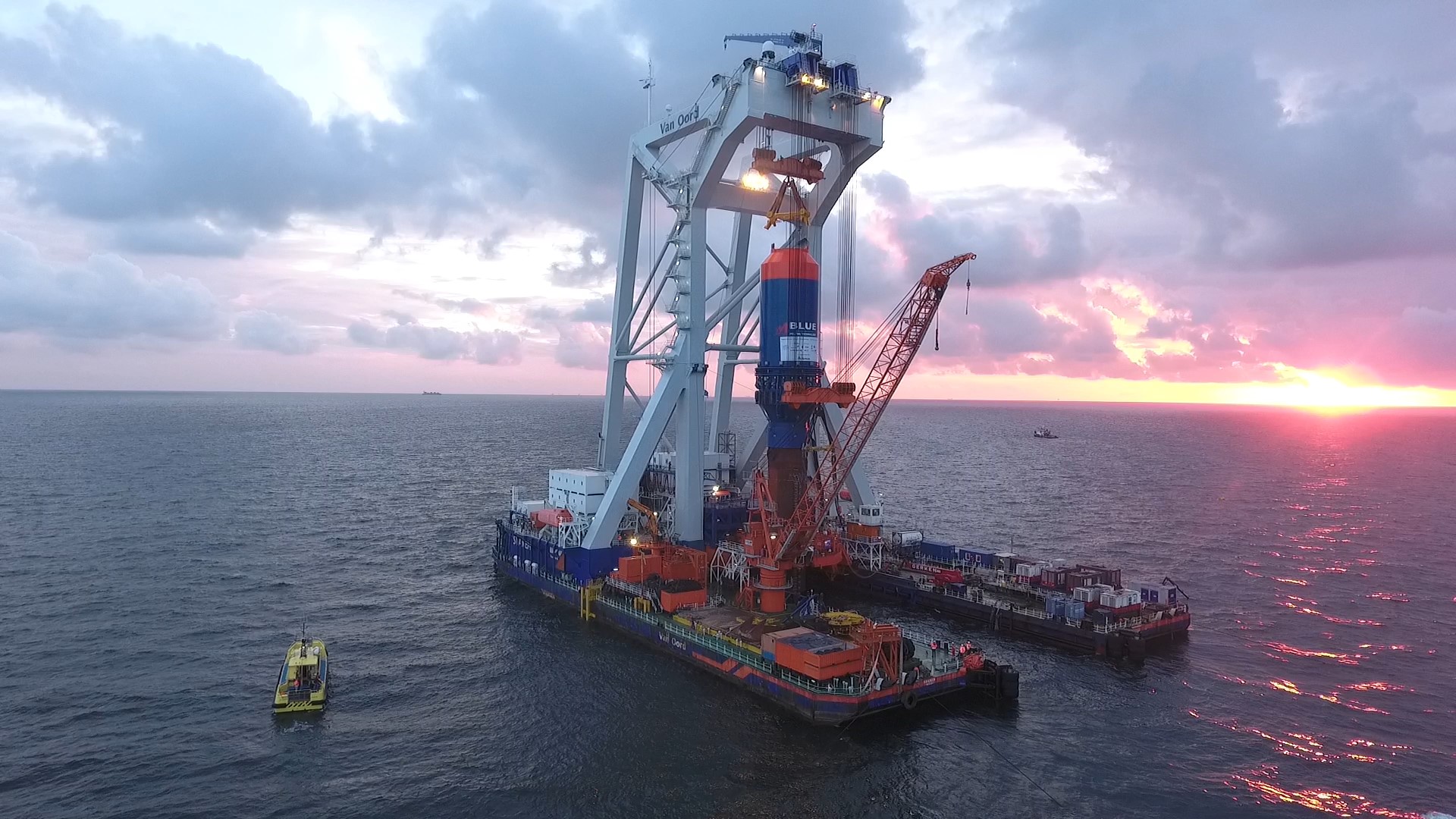
Fatigue Analysis
We perform fatigue analysis regularly on structures and equipment. Read more about our approach to this technique.
How we can help you
At HVR Engineering we believe that understanding a process is essential to deliver accurate and realistic results. Our experience with transport and fatigue analysis allows us to cover the complete process from A to Z, which means we do not work with 3rd party ‘black box’ information.
Want to know what we can do for you? Read more about our FEM services or get in touch!