Pile Drivability Fatigue
The rise of Offshore Wind
A great development over the last years has been achieved by the wind energy with an average growth of the cumulative wind power capacity of c.a. 40% from the end of 2013 to the end of 2017.
The drive for this development is to meet the continuous demand for energy and the necessity of having sustainable energy supply, and this growing trend is expected to continue in the coming years with more and more offshore wind farms installed every year.
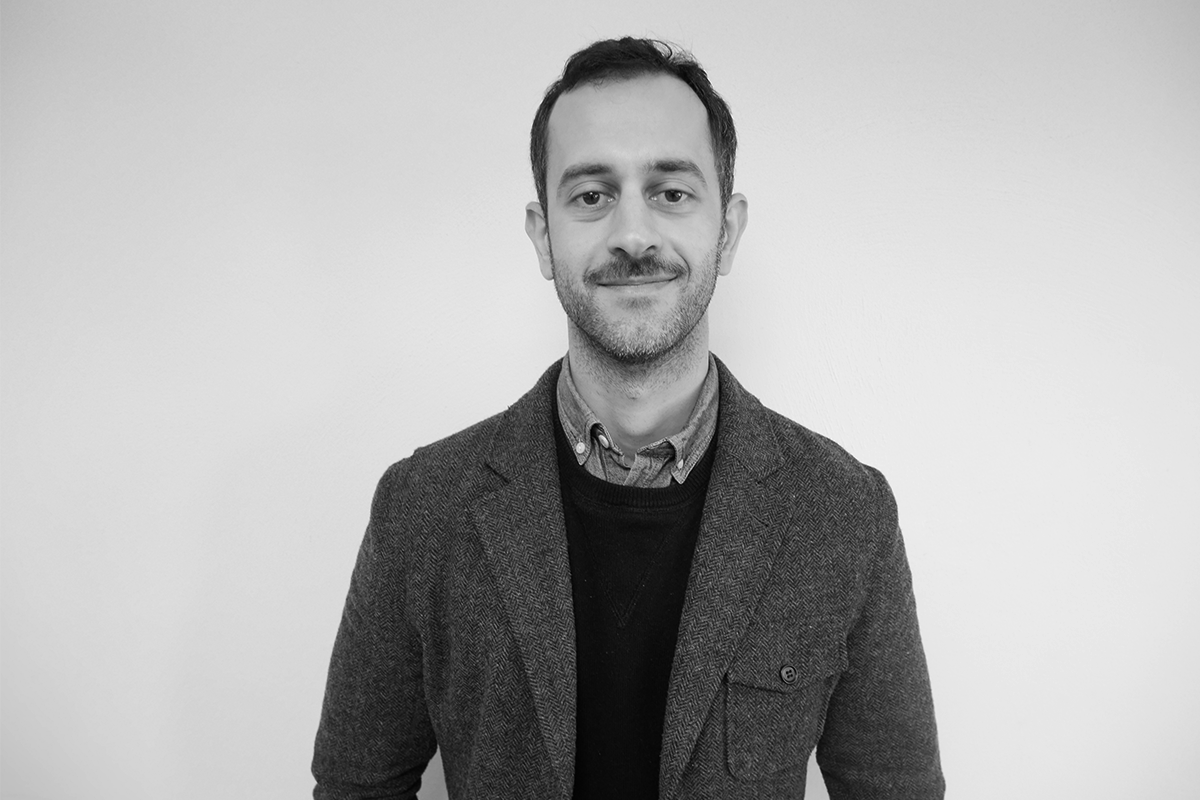
Michele Orlando
Lead Engineer Strength and Fatigue
"It is clear that improved assessment methods are required to calculate more accurate fatigue damages during pile driving."
Monopile foundation installation
For offshore wind turbines installations, also depending on the water depth of the installation, the most efficient foundation design is represented by the monopile foundation. A standard monopile design consists of a welded steel pipe built up with both tubular and conical sections, representing a more a simpler layout compared to more complex structures such as tripods or jackets.
Dynamic effects of impact hammers
Usually, monopiles are installed by the means of impact hammers that exert high dynamic loading on the structure to be able to drive the pile at the required soil penetration. During this structurally demanding operation, a significant amount of cumulative fatigue damage can rise in the construction which will cause a reduction of the in-service fatigue life. Currently, standard design assessments against fatigue damage are performed by the use of commercial software based on mono-dimensional wave equation analysis including the effects of structure-soil interaction, hammer impact energies and number of impact blows.
Improving fatigue calculations
Normally, these simplified 1D analyses represent the starting point of simplified stress-based fatigue calculations based on longitudinal stresses only adopting the S-N curves of relevant standards such as the DNVGL-RP-C203 recommended practice that cannot account for the effects of local bending and local vibration of the monopile, typical of flanged construction used to connect the monopile to the transition piece or tower. Considering today’s developments in the wind offshore industry, with more and more advanced connection methods between the monopile and the transition piece/tower, it is clear that improved assessment methods are required to calculate more accurate fatigue damages during pile driving.
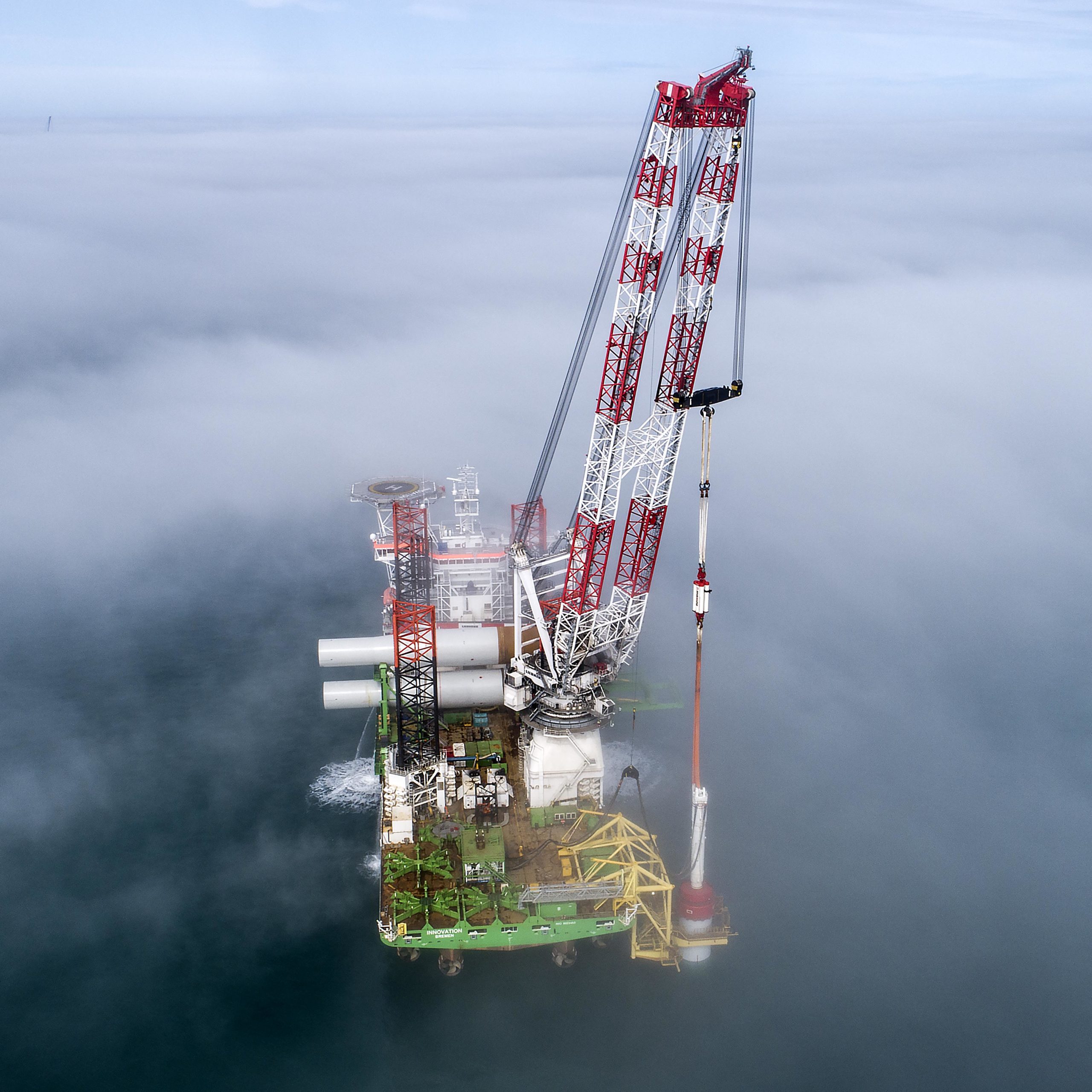
Pile driving fatigue methodology
HVR developed over the last years a pile driving fatigue methodology based on refined two and three dimensional FE calculations, focusing in particular on the top part of the monopile where the effects of distortion/vibration induced fatigue are more dominant.
The mentioned fatigue assessment method accounts for several variables, such as the effects of soil friction during driving and manufacturing tolerances, also addressing the problem of incremental plastic failure during pile driving by the application of nonlinear kinematic hardening material models.
This refined fatigue analysis methodology was also presented at the WESC 2021 conference.
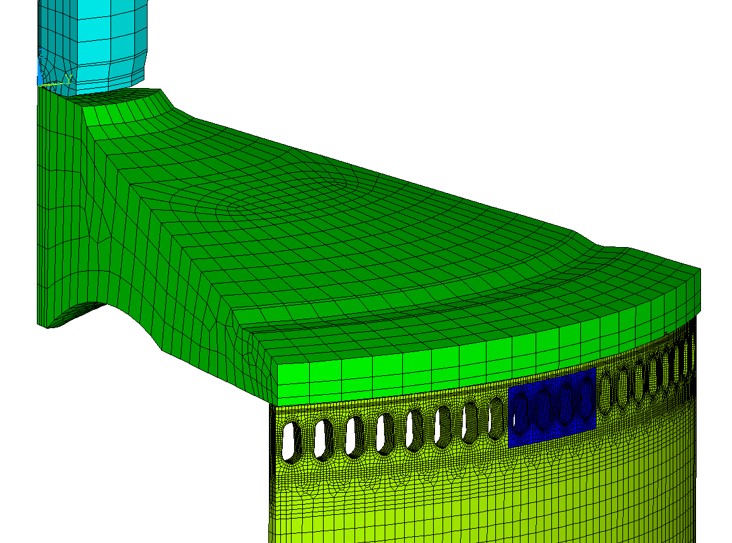
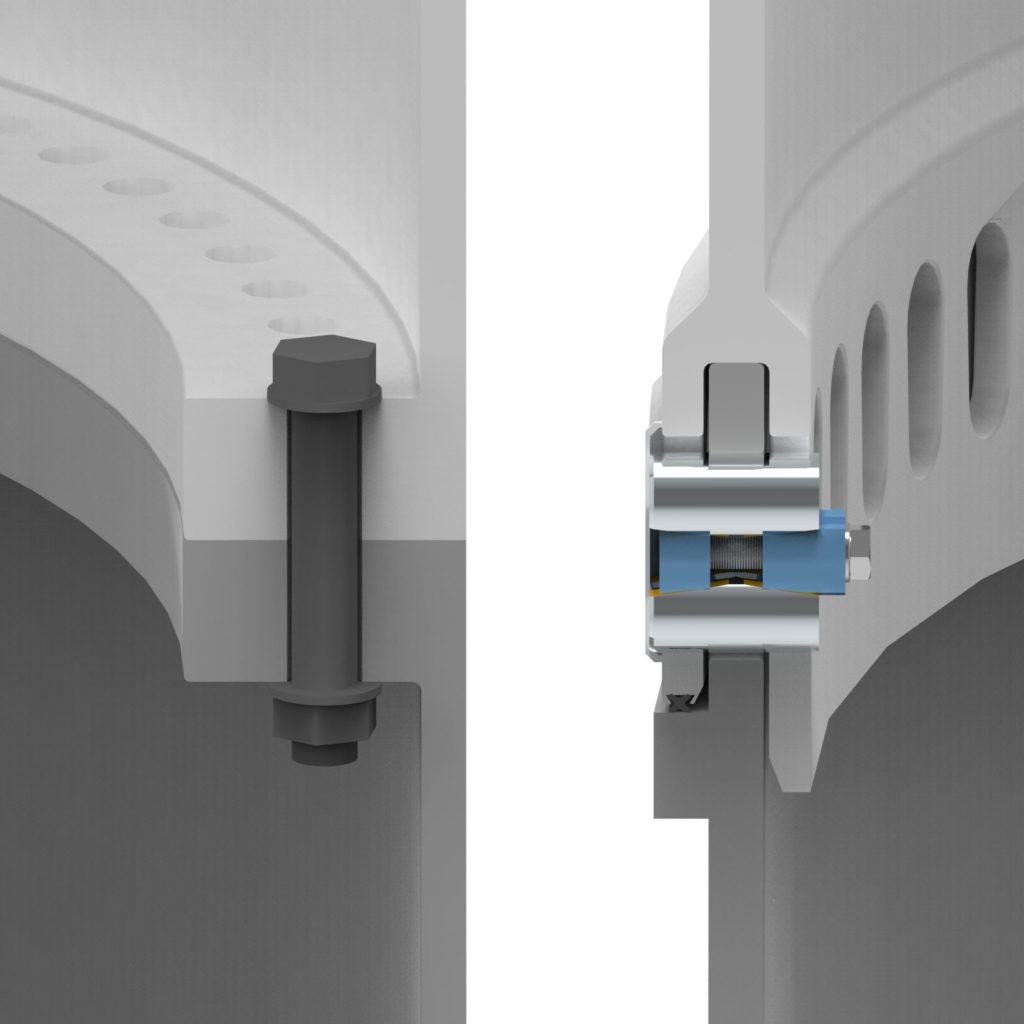
Pile drivability analysis
We used our methodology for Pile Drivability on the C1 Wedge Connection, a new monopile interface connection.
How we can help you
Our approach to pile drivability fatigue is one example of our capabilities of coupling dynamic analyses with detailed fatigue calculations, executed with a practical view but in strict accordance of the first engineering principles that are the base of the real behaviour of structures and materials!
Have a look at our FEM services page for more information on how we can assist on your projects with strength and fatigue expertise